Reducing the environmental impact in building projects
Innovations in the future of sustainable concrete
The construction industry is a massive consumer of raw materials and natural resources, and there's a growing need to reduce the environmental impact of building projects. As a widely used construction material, concrete has a significant role to play in this. By incorporating sustainable practices and considering the environmental impact throughout the lifecycle of concrete structures, the industry can contribute to a more sustainable built environment.
Concrete and sustainability – the issues and opportunities
Concrete often gets bad press when it comes to sustainability, but it's the cement content that's the main issue. Cement is the common “binder” material which bonds the rest of the aggregates together – but it needs to be fired during its manufacture, which makes the process very energy intensive; all of the other ingredients of concrete carry relatively low emissions. Despite making up around just 10-15% of its content, cement usually accounts for over 80% of the carbon footprint of a concrete product. However, cement content aside, concrete does have lesser-known carbon benefits.
The main benefit is that it naturally absorbs CO2 from the atmosphere over its lifespan – a process known as carbonation. Carbonation occurs more readily in concrete structures that are exposed to the open air or have a higher moisture content – meaning this is particularly relevant for the external walls and exterior landscaping. When it comes to making concrete more sustainable, there are several opportunities, including improving energy efficiency during production, reducing its cement content, and capitalising on carbon absorption benefits.
Removing cement from concrete
The negative contribution cement makes to concrete's carbon footprint motivates innovative developments to reduce and remove it. Manufacturers, suppliers and partners from across the concrete industry are making these sustainable changes, driven not only by legislative requirements and growing pressure from the construction industry, but also by their own pursuit towards a greener future. Developing cement-free concrete involves eliminating the use of Ordinary Portland cement, a major contributor to carbon dioxide emissions during production. There are a number of different ways to approach this, including exploring alternative binders and innovative activator solutions.
Case study – cement free concrete paving
As a leading UK-based building materials and hard landscaping manufacturer, Marshalls supplies a range of concrete products, from paving to drainage. The business has been researching and developing cement free concrete for some time, focussing on maintaining quality whilst reducing environmental impact.
Marshalls cement free concrete has been developed to significantly reduce the carbon embodiment generally associated with using standard cement and cement clinkers based concretes. The production of Ordinary Portland Cement is estimated to release in the region of 780kg of CO2 per tonne of cement produced into the atmosphere. By comparison, the cement free binder systems developed for Marshalls have between 75 & 150kg of embodied carbon per tonne of binder.
Marshalls is working with several suppliers to utilise by-products from other industrial processes and waste materials that, when activated, give similar chemical reactions and properties to cement based systems. The ‘glues’ that hold it all together are activators that are based on a blend of raw materials that, when used in conjunction with the cement replacement materials, react chemically and produce concrete with the strength and durability performance of conventional concrete.
While Marshalls is currently focusing this innovation on block pavers, it will be trialled across other concrete products in pursuit of a carbon-negative concrete.
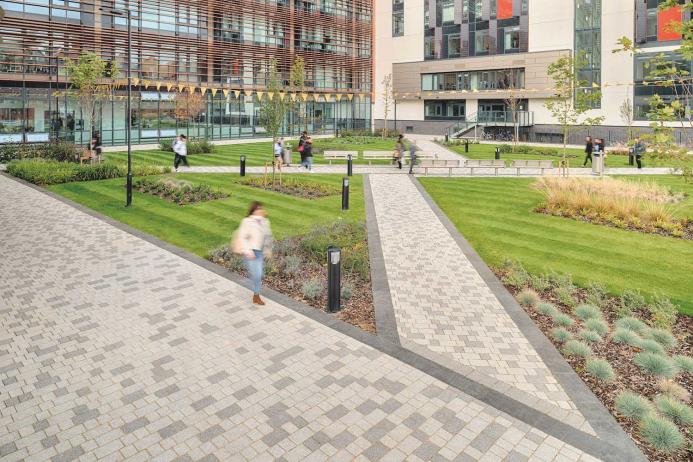
Using carbon capture technologies with concrete
Concrete naturally reabsorbs (or "sequesters") carbon over its lifetime. This is a permanent carbon capture process; on contact with cement in the concrete mix, CO2 mineralises to create calcium carbonate. Once mineralised, the CO2 is permanently locked into the concrete and will never be released – not when it is crushed or degrades in thousands of years. Carbon capture involves capturing CO2 emissions from their sources, transporting them, and then storing or burying them in suitable deep underground locations. There are two primary methods for storing CO2: deep geological storage and mineral storage.
In mineral storage, the captured CO2 is reacted with naturally occurring minerals like iron, magnesium, and calcium. This process, known as mineral carbonation, mimics the natural carbonation that happens over time and is highly stable, preventing the CO2 from being released back into the atmosphere. By utilising materials such as cement, which contain mineral-rich components (e.g., oxides), this mineral storage approach can be replicated on a smaller scale, effectively sealing the CO2 within concrete, thereby providing a permanent solution.
Case study – Carbon capture within concrete bricks
In August 2022, Marshalls launched a trial using CarbonCure technology with concrete bricks, becoming the UK's first precast concrete masonry producer to use the system. This technology works by injecting CO2 into the concrete mix, driving carbon into the fabric of the block right at the start of its manufacture. As well as preventing that carbon from entering the atmosphere, the chemical reaction of turning the calcium oxides within the cement into calcium carbonates, offers increased performance giving us the ability to reduce the cement content. As cement carries around half of the carbon in a standard concrete brick this is an additional benefit. During the trial, captured CO2 emmisons from local industry were used.
Marshalls has since adopted the technology for all facing bricks manufactured at its Grove site, in South Wales, and recently launched Glenwall, its first new facing brick range using the technology. Marshalls estimates that this project prevents 30,000kg of CO2 from entering the atmosphere in the first year alone. Whilst this is a relatively small saving, it's enabling them to prove and maximise the technology at scale before rolling it out to other products and sites.
Summary – the impact of making concrete more sustainable.
Summary – the impact of making concrete more sustainable
For building projects, concrete remains a versatile, durable, cost-effective material for which a suitable alternative has yet to be found. It’s clear, then, that low-carbon concrete provides one of the biggest single opportunities to reduce global carbon emmissions – and it stands to reason that the first businesses to pioneer new, cleaner concrete technologies stand to make the biggest gains in the race for a truly sustainable future.
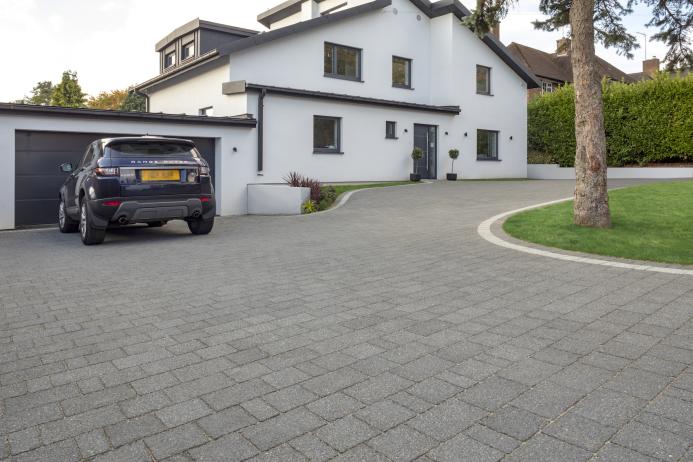